Chapter One: Globes
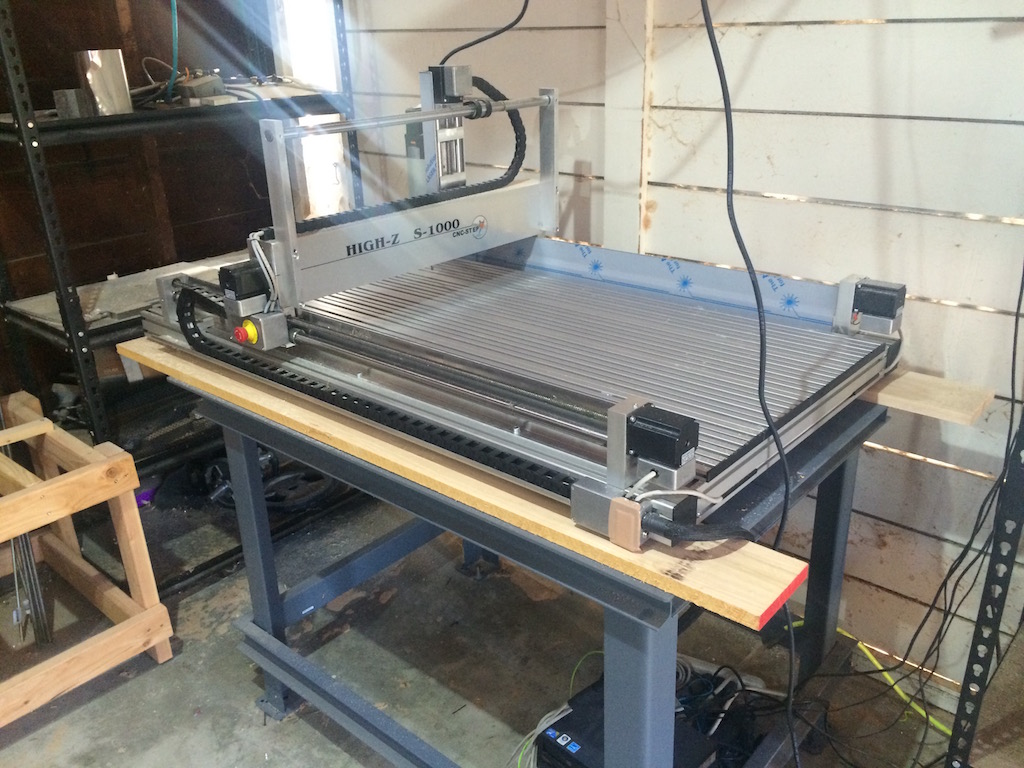
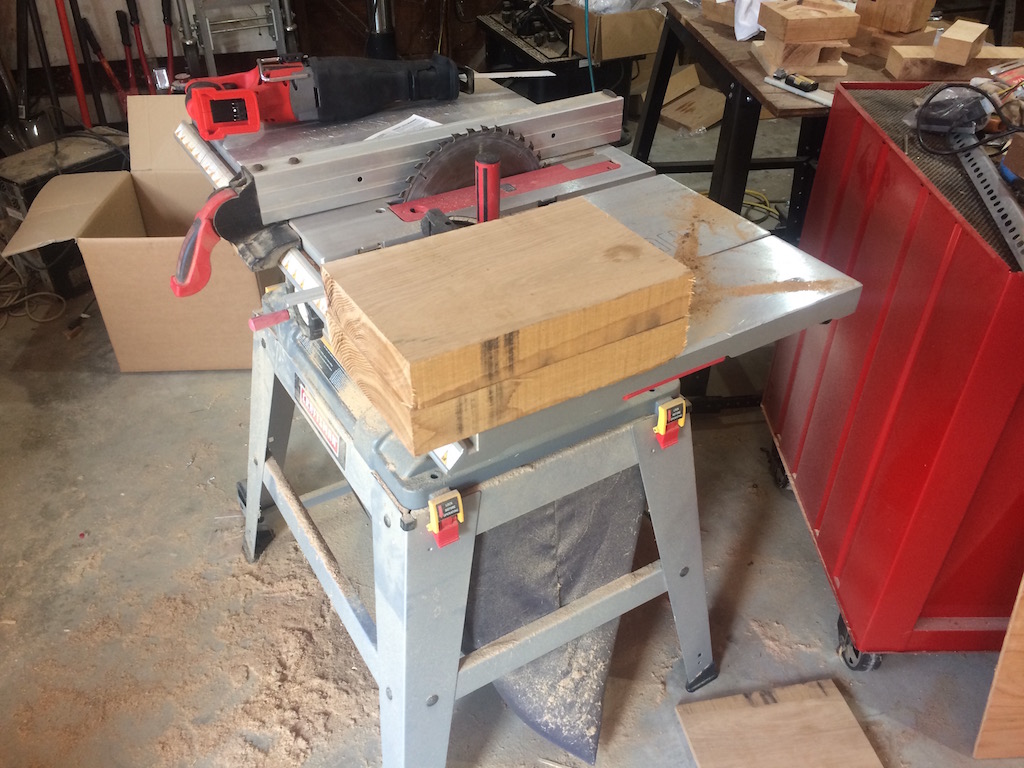
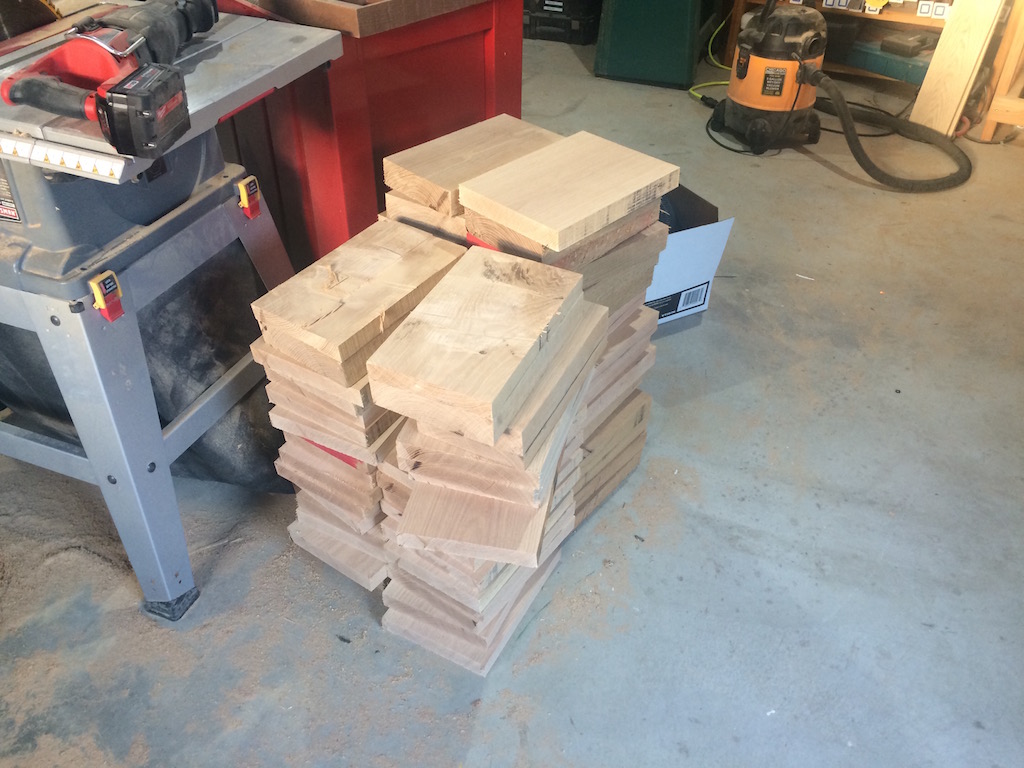
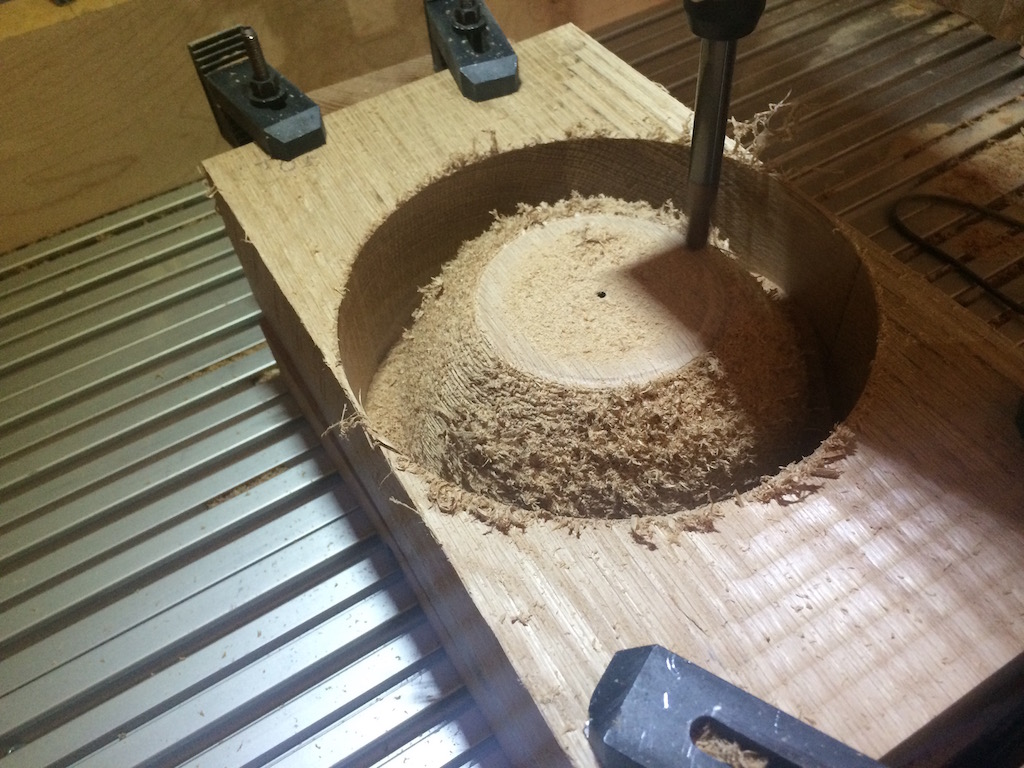
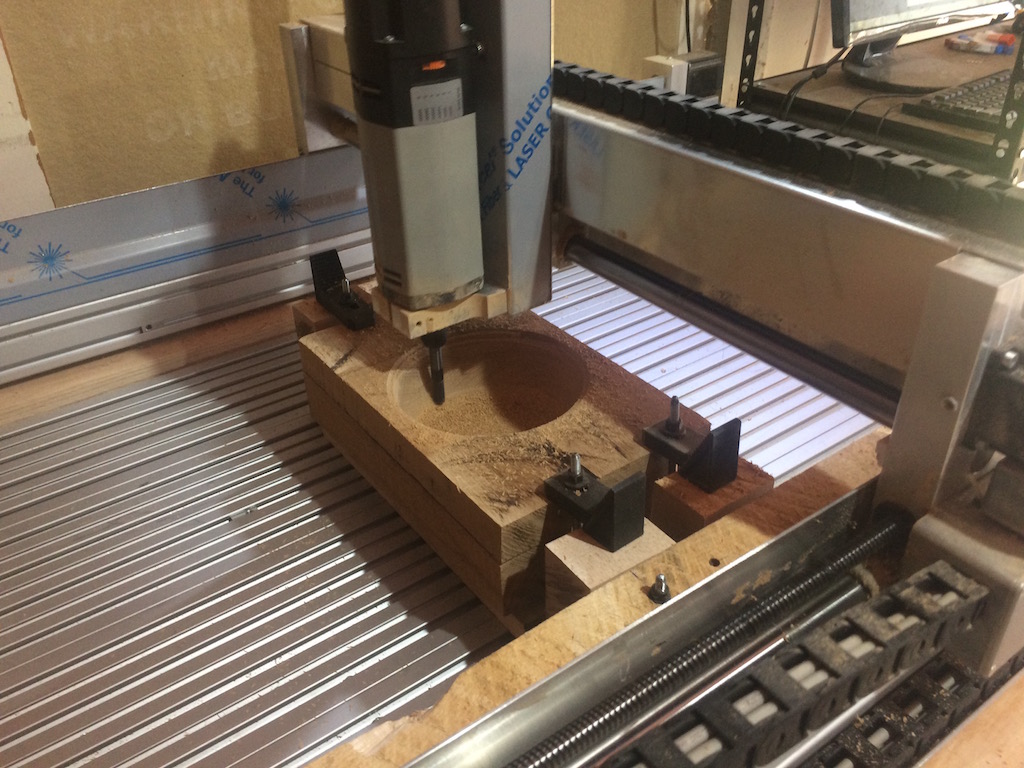
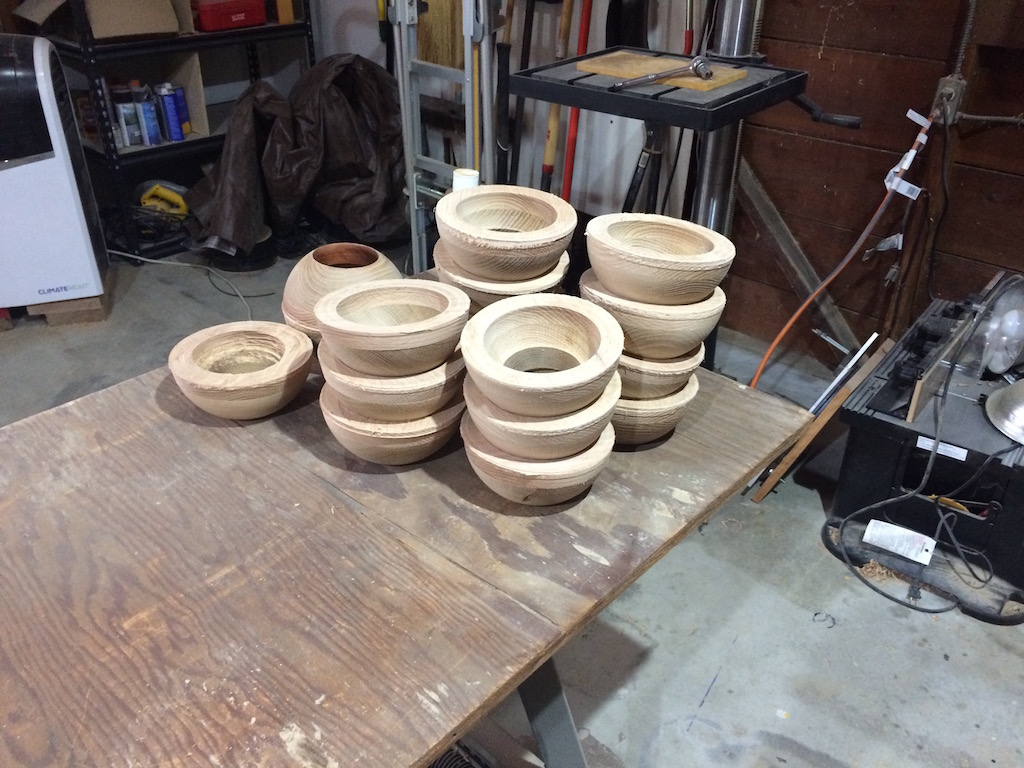
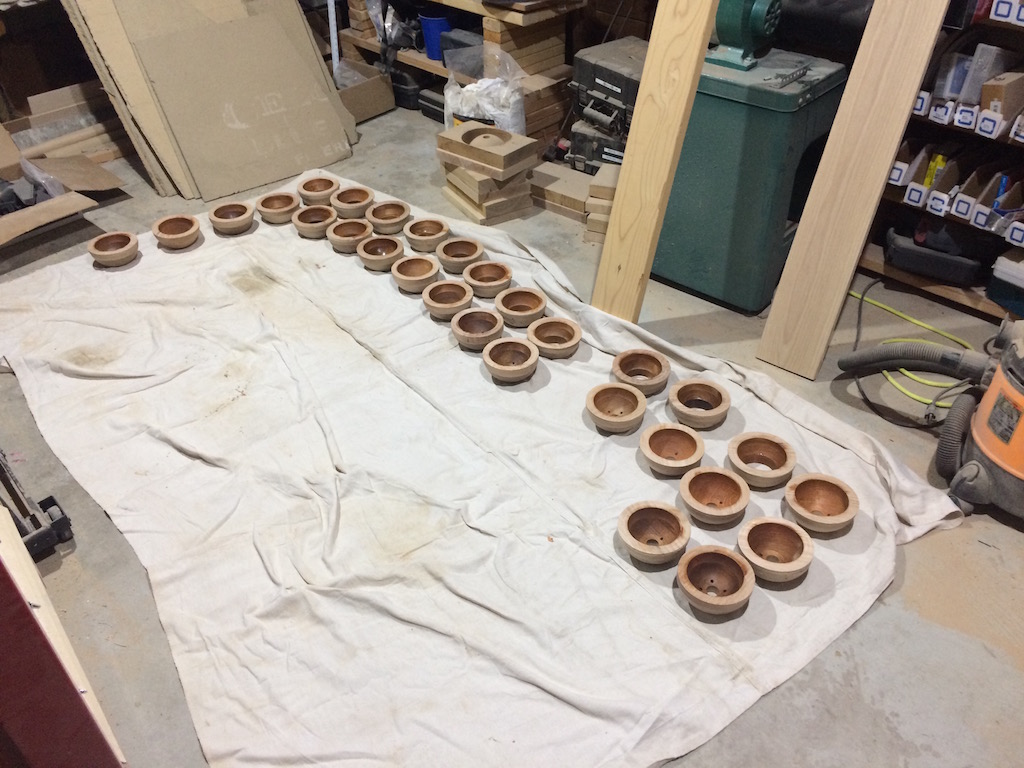
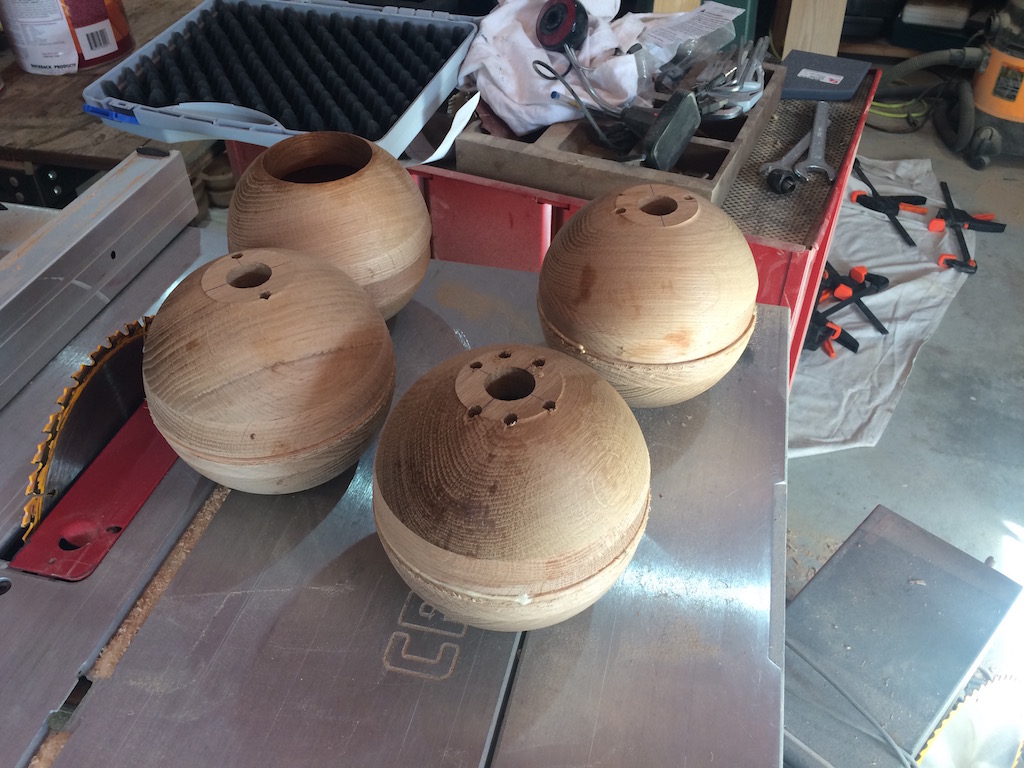
Chapter 2: How To Make A Butterfly
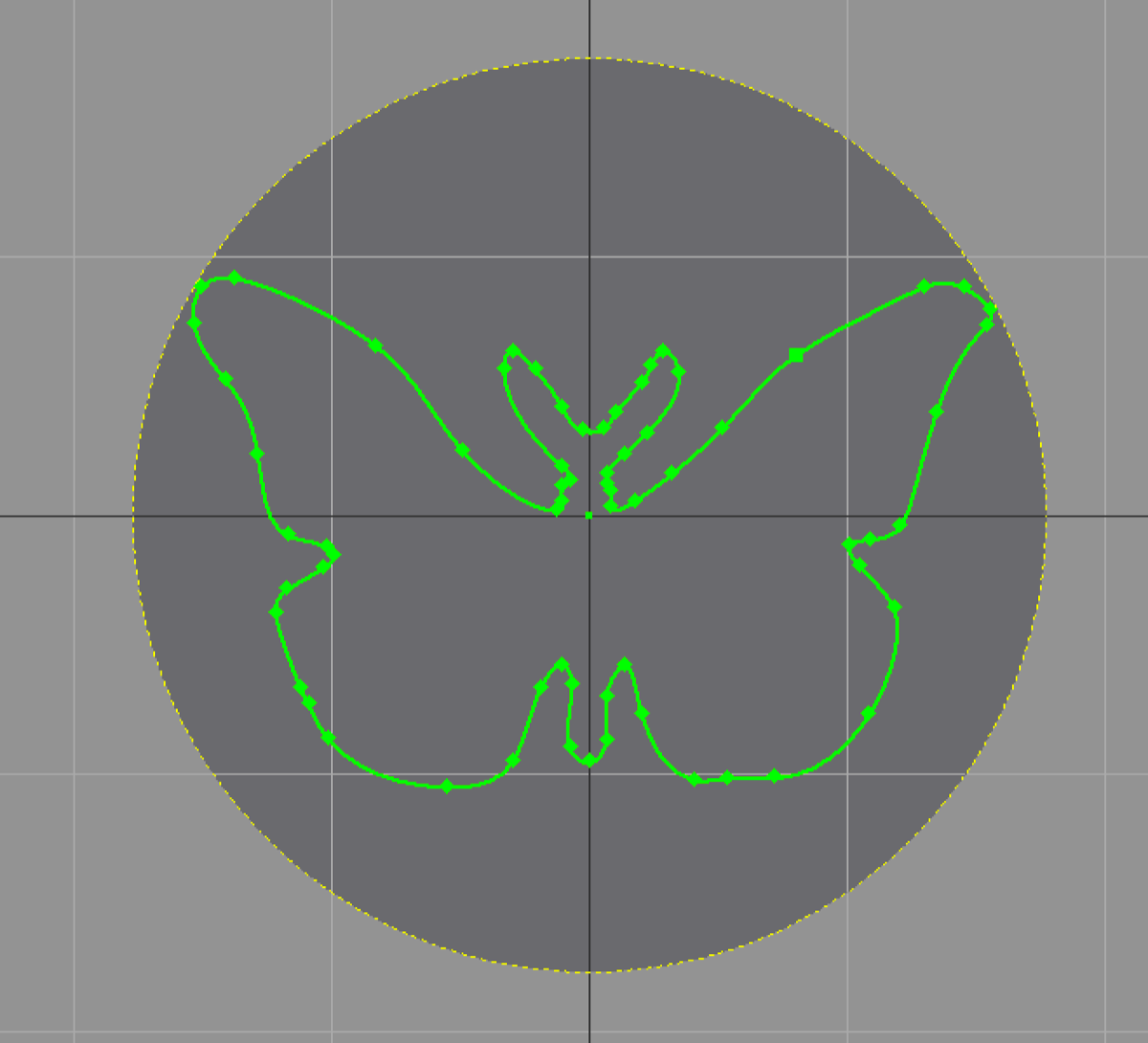
Draw or trace yourself a butterfly.
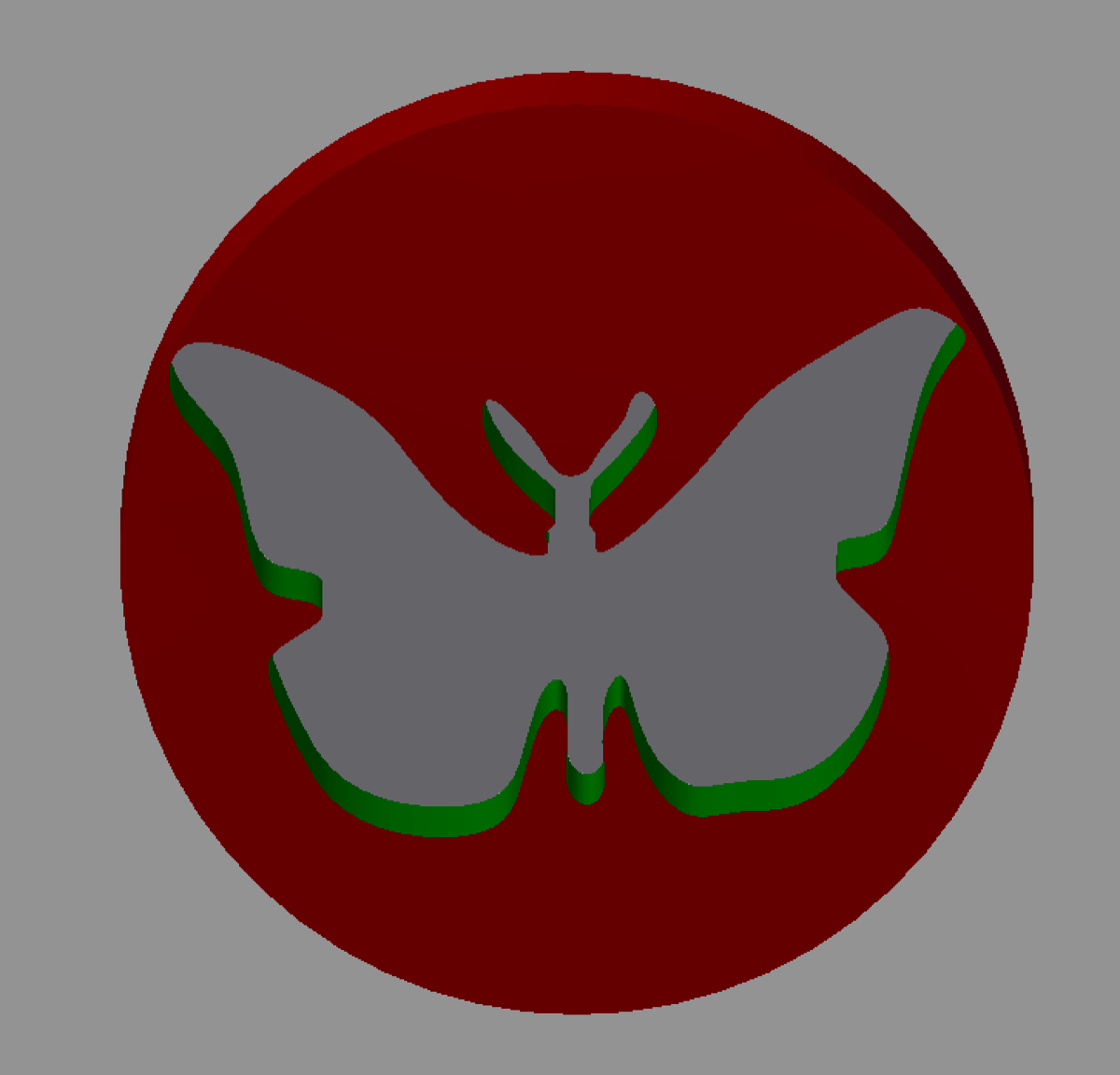
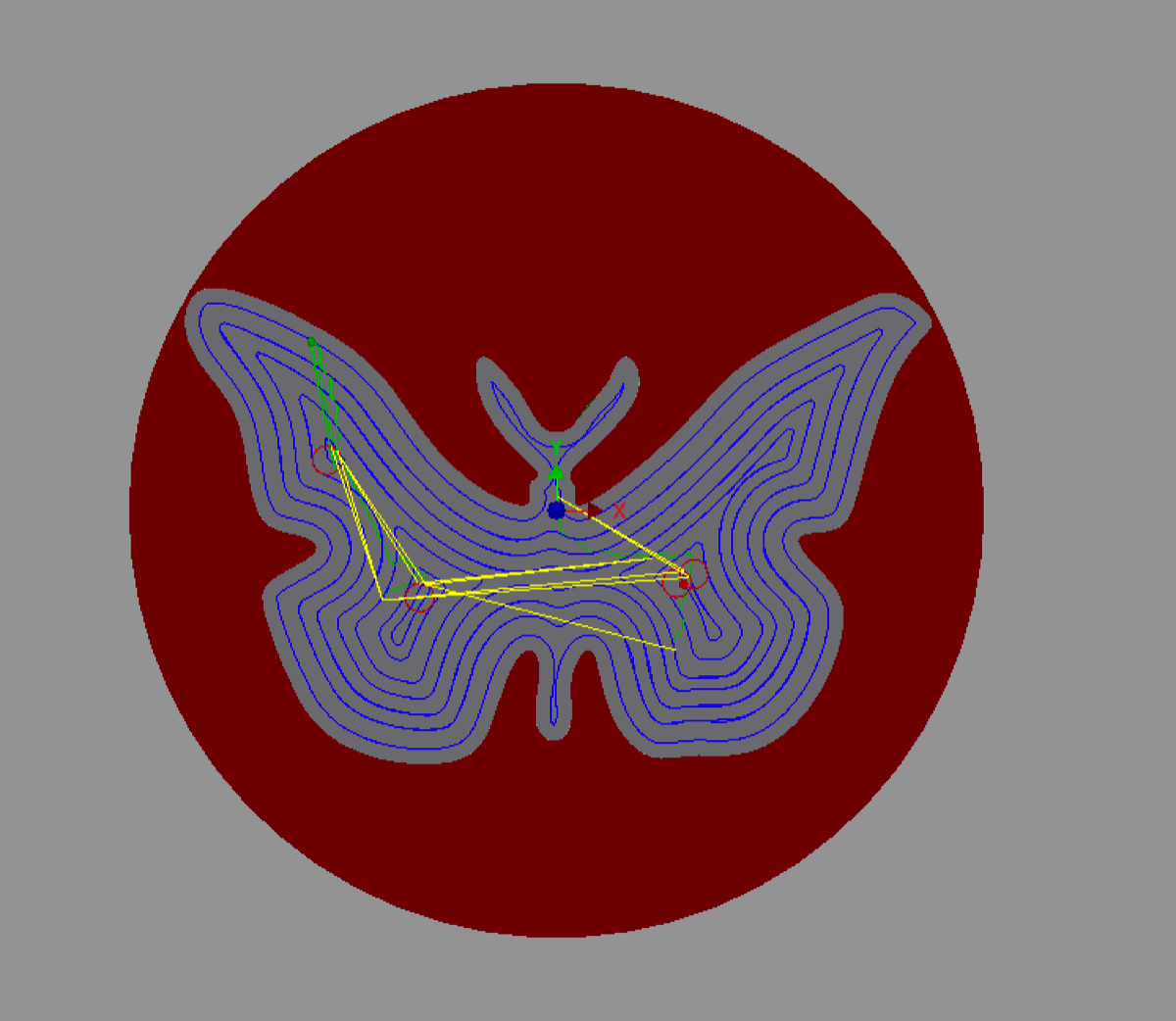

[A quick diversion for my math loving friends. The cylinder has a radius of 45mm and we can treat the wings as if they touch the edges. The globes have a 75mm total radius with a shell thickness of 20mm. Cutting from the globe surface, how deep does the cylinder need to be to make sure that the entire butterfly cuts through to the inside of a globe? Extra credit — it we take out the whole cylinder what is the total amount of material removed by the cut?]
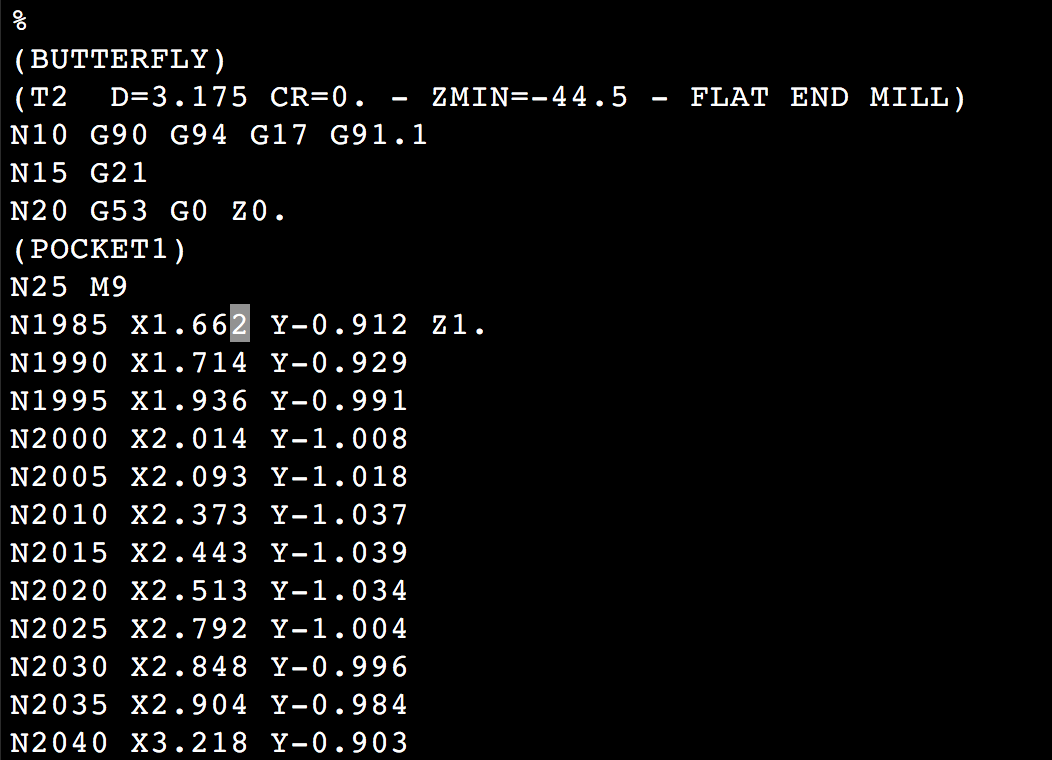
G-code is what is generated by the drafting software and read by the machine controller.
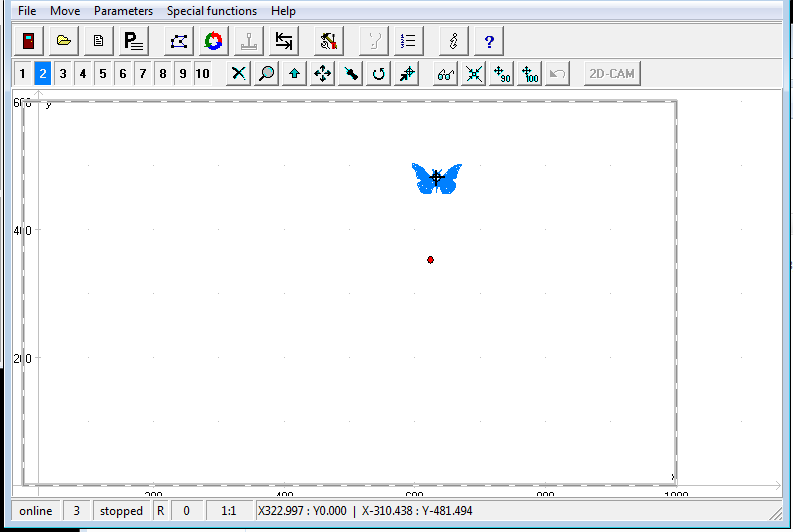
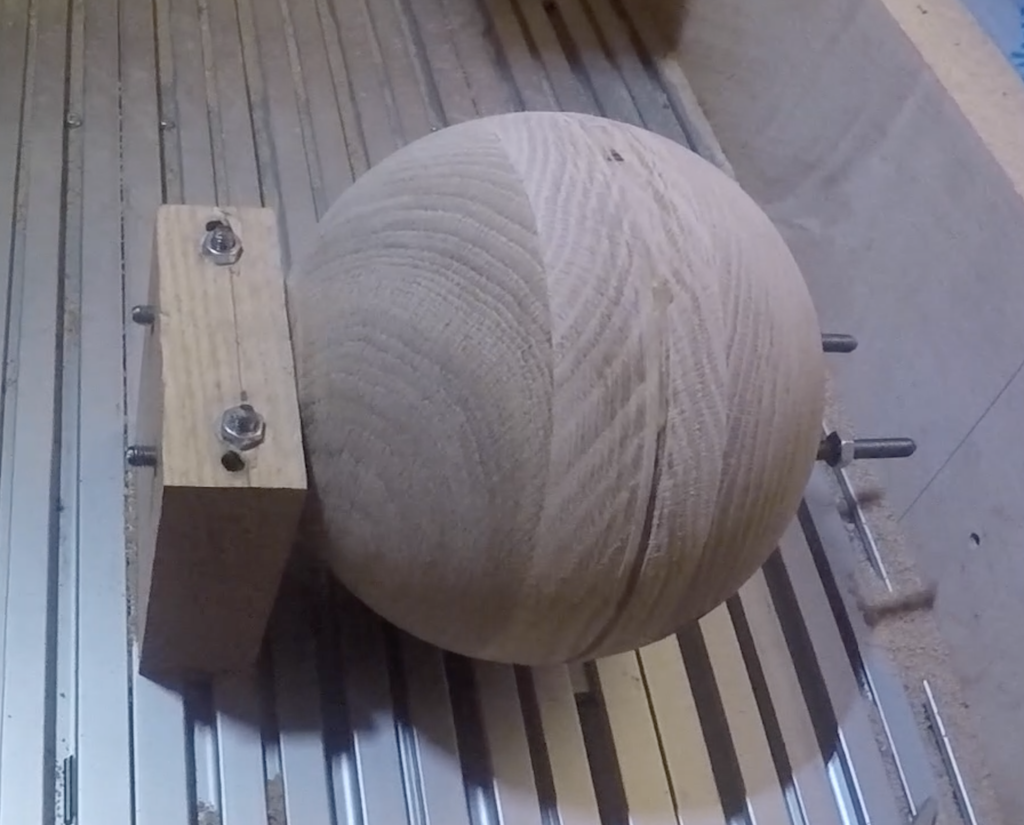

End mills look a lot like drill bits except that they don't have pointy ends. They are meant to cut from side to side rather than up and down.
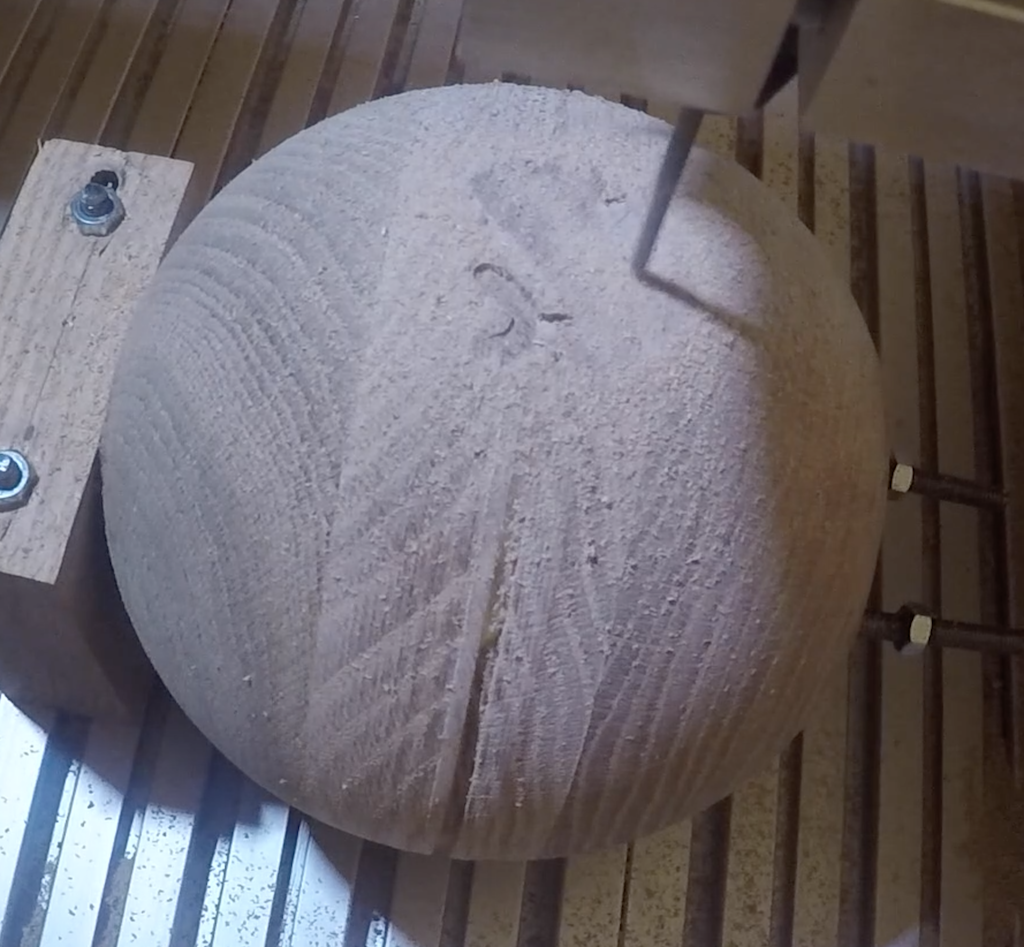
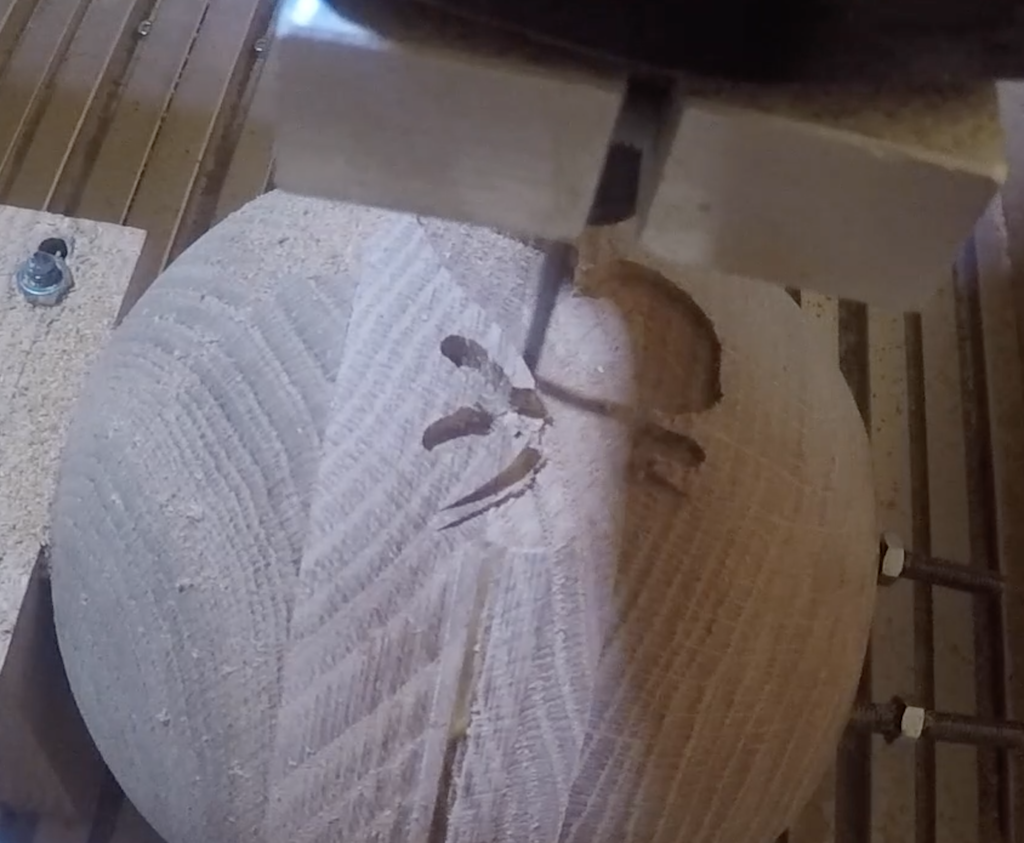
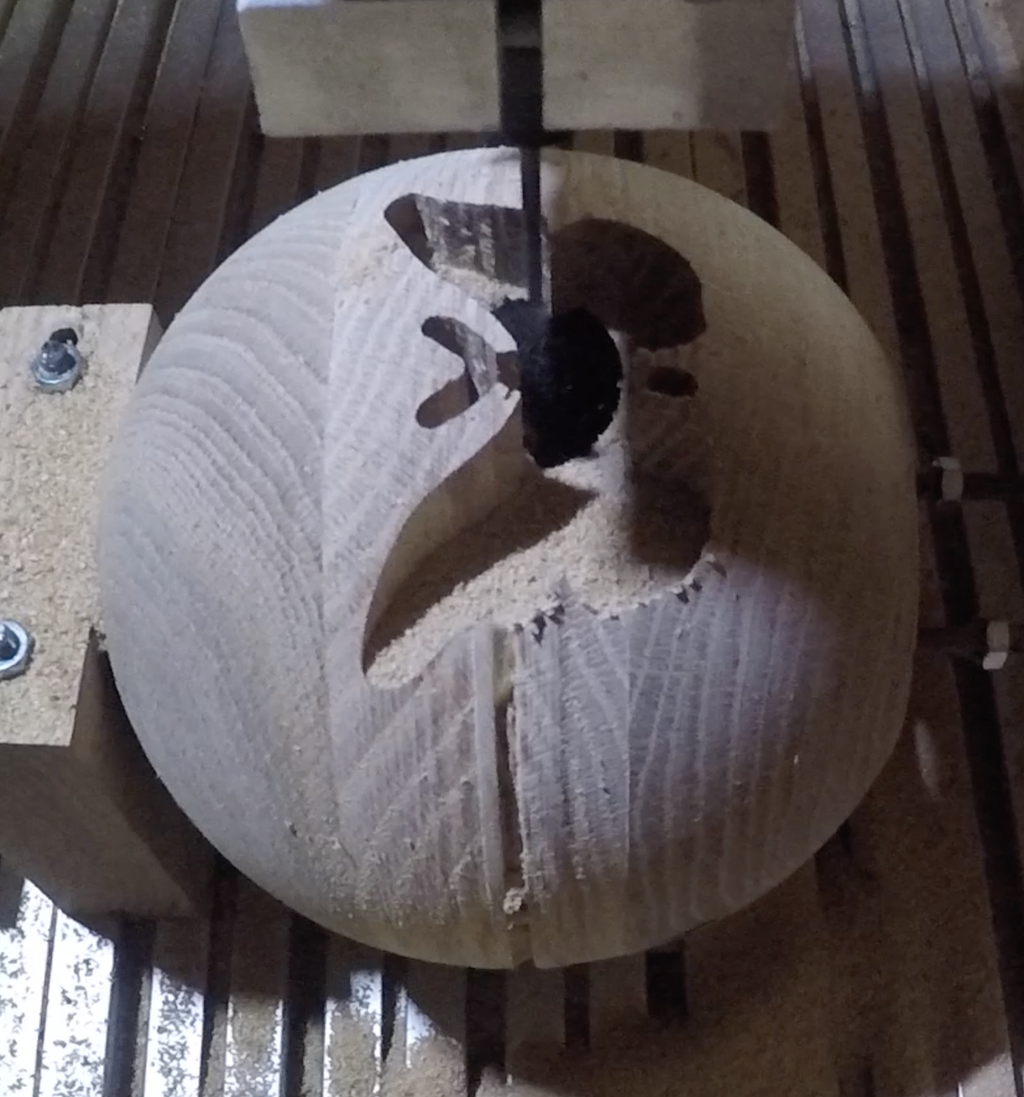
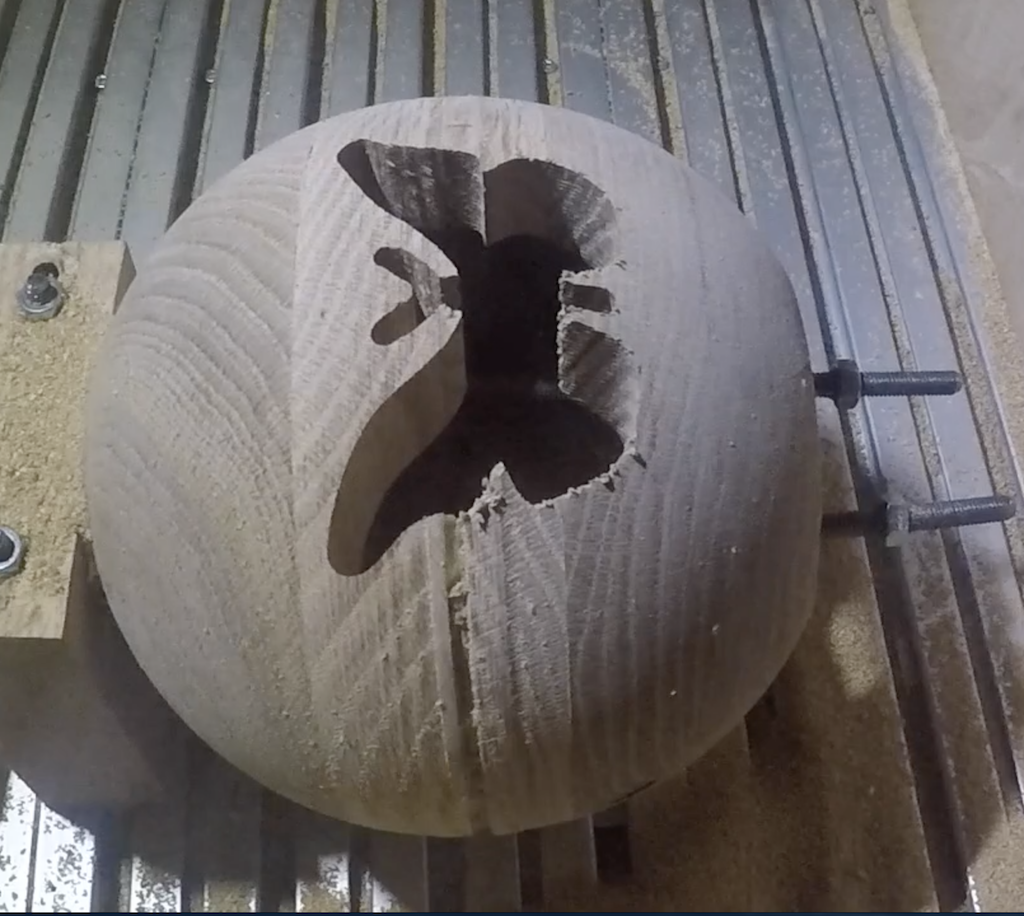